Каталитические реакторы для дожигания отходящих газов
Каталитические реакторы для дожигания отходящих газов
Каталитические реакторы
для дожигания отходящих газов
Батура П. И.
Для очистки промышленных газовых выбросов от
органических примесей и вредных сернистых соединений применяют различные
методы: абсорбционные, термические, адсорбционные, каталитические и
комбинированные. Наиболее перспективные — термические и каталитические методы
обезвреживания органических примесей в газовых выбросах химических,
коксохимических, металлургических заводов и других предприятий. Они надежны,
дешевы и достаточно эффективны [1—3].
Процессы глубокого термокаталитического окисления
проводят в специальных реакторах, которые обычно работают в двух режимах:
стационарном и нестационарном. Термокаталитические реакторы производительностью
5, 10 и 25 тыс. м3/ч разрабатывает Институт газа АН УССР. Они отличаются
компактностью, простотой в изготовлении и надежностью.
Реактор представляет собой конструкцию башенного типа,
включающую многоходовой трубчатый воздухоподогреватель — рекуператор, встроенный
смешивающий воздухоподогреватель и газовую горелку, в верхней части размещена
каталитическая камера (рис. 1). Реактор оборудован системой КИПиА, позволяющей
выполнять по заданной программе пусковые и остановочные операции, а также
поддерживать оптимальный тепловой режим с соблюдением требований безопасности.
Реакторы производительностью 5 и 10 тыс. м3/ч с платиновым катализатором
внедрены и успешно работают [4].
В Дзержинском филиале НИИОгаза (г. Дзержинск
Горьковской обл.) выполнены работы по обезвреживанию газов от окислительных
колонн синтеза жирных кислот [5]. Установка производительностью 25—30 тыс. м3/ч
включает двухполочный реактор и два теплообменника. Температура газов в I
ступени 190—200, во II 240— 450 °С, а на выходе из слоев катализатора достигает
соответственно 250—450 и 330—580 °С. Высота слоя катализатора 300—350 мм,
линейная скорость потока газов приблизительно 1 м/с, степень очистки после II
ступени 99 %.
Имеются данные о реакторе, работающем в нестационарном
режиме, т. е. в режиме переключения направления потока реакционной смеси. В
таком реакторе можно проводить обезвреживание разбавленных органических
выбросов и оксида углерода [6, 7]. На рис. 2 представлен реактор с
катализатором на сетке, предназначенный для окисления метанола [8].
Самым простейшим аппаратом является реактор с
неподвижным слоем катализатора (рис. 3). Однако в нем трудно равномерно
распределить поток газов и избежать градиентов температуры по слою
катализатора, а также предотвратить разложение реагентов на перегретых участках
при снижении скорости реакции на ненагретых. Более сложен полочный реактор с
несколькими слоями катализатора (рис. 4). В нем поток газа лучше распределяется
и охлаждается между слоями, причем можно вводить горячий и холодный газ, а в
разных слоях поместить разные катализаторы; кроме того, можно избирательно
заменять слой дезактивированного контакта и поддерживать различную температуру
в слоях.
В работе [9] приведены результаты моделирования
каталитического реактора очистки отходящих газов лакокрасочного производства. В
газах концентрация органических примесей не превышала 500 мг/м3 (циклогексан,
н-ксилол, пентан и др.). Даны рекомендации по выбору оптимального режима и
экономики процесса. Основные данные: сопротивление системы не более 4 кПа, высота
слоя катализатора 50—200 мм; температура процесса 425—450 °С, скорость газа в
реакторе 0,6 м/с, время контакта 0,12 с.
Реактор производительностью 50 тыс. м3/ч разработан
Дзержинским филиалом НИИОгаза и серийно изготовляется заводом химического машиностроения
(г. Пенза). Его диаметр 500 мм, высота 2200 мм.
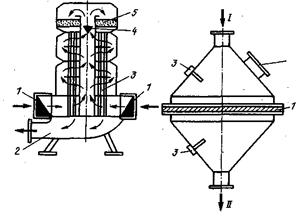
Рис. 1. Термокаталитический реактор:
1— входные патрубки; 2 — выходной канал; 3 —
теплообменник; 4 — газовая горелка; 5 —катализатор
Рис. 2. Реактор с катализатором в виде сетки:
1—сетка; 2—люк и смотровое окно; 3— термопары; I,
II—соответственно вход и выход газов
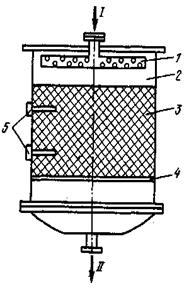
Рис. 3. Реактор с неподвижным слоем катализатора:
1—газораспределитель; 2—камера смешения;
3—катализатор; 4— решетка; 5 — термопары; I—ввод газов; II—очищенные газы
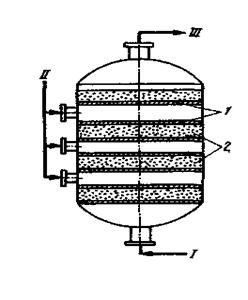
Рис.4. Полочный реактор:
1-опорная сетка; 2-слой катализатора; I-ввод газов;
II-ввод холодного воздуха; III-очищенные газы
Институтом газа АН УССР совместно с конструкторским
бюро и мастерскими опытного производства разработана установка, действующая на
комбинате печати “Радянська Україна”. Основные данные реактора: объем
катализатора 0,4 м3, температура процесса 380 °С, сопротивление 1,8 кПа;
габариты 3,5*3,5*8 м, масса установки до 6 т.
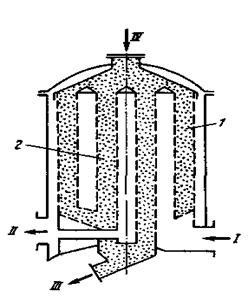
Рис. 5. Реактор с двухкольцевым размещением
катализатора:
1— корзины с катализатором; 2 — внутреннее кольцо с
катализатором; I, II—соответственно вход и выход газов; III—выгрузка
катализатора; IV—загрязненные газы
Минский конструкторско-технологический
экспериментальный институт разработал простейшие реакторы УСК-39, УСК-41 и др.
На рис. 5 показан реактор с двухкольцевым размещением катализатора конструкции
Дзержинского филиала НИИОгаза. В этом же институте создан реактор для дожигания
газов от сушильных камер окрасочных линий машиностроительных заводов (рис. 6).
Подача газов осуществлена по кольцевому каналу, где они смешиваются с дымовыми
газами от сжигания жидкого или газообразного топлива.
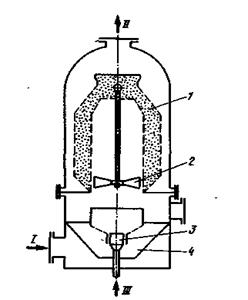
Рис. 6. Реактор:
1—катализатор; 2—воздухораспределитель; 3—горелка, 4 —
распределитель газов; I—ввод газов; II—очищенные газы; III—топливо
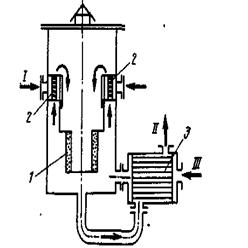
Рис. 7. Каталитический реактор:
1—катализатор; 2—панельные горелки; 3—кожухотрубчатый
теплообменник; I—природный газ; II, III—соответственно выход и вход газов
В аппарате Гипрогазоочистки (рис. 7) газы поступают в
трубное пространство теплообменника и далее в реактор, где смешиваются с
дымовыми газами сжигания топлива в панельных горелках, проходят через слой
катализатора, а затем через межтрубное пространство теплообменника сбрасываются
в атмосферу. Аппараты, представленные на рис. 6 и 7, прошли промышленные
испытания и хорошо зарекомендовали себя в рабочих режимах.
Наиболее многочисленны реакторы со встроенными
рекуператорами тепла типа ТКВ. Технические характеристики таких реакторов
приведены в работе [10].
Подобные аппараты применяют в Польше; они разработаны
Проектным бюро охраны природы “Проат” (рис. 8). В Германии создан реактор типа
КВ, в корпусе которого размещен слой катализатора и теплообменник (рис. 9).
Разработано пять типоразмеров таких реакторов производительностью от 5 да 25
тыс. м3/ч. Иногда рекуператор тепла примыкает к реактору. Такие установки
имеются в ФРГ и Англии. В Венгрии, Франции и США внедрены установки с верхней
подачей газа по кольцевым каналам [11].
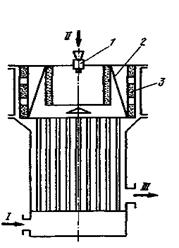
Рис. 8. Реактор типа ТКВ:
1—горелка; 2—отражатель; 3—катализатор; I—ход газов;
II—топливо; III—очищенные газы
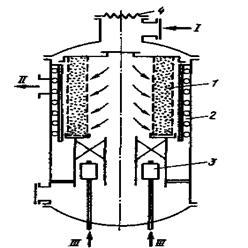
Рис. 9. Реактор типа КВ:
1—катализатор; 2—теплообменник; 3—горелка;
I—загрязненные газы; II—очищенные газы; III-топливо
Имеются данные о работе опытно-промышленной установки
для очистки газов, которая разработана в Ленинградском технологическом
институте совместно с Институтом катализа СО АН СССР. Температура в слое
катализатора достигает 450—500 °С.
Таким образом, каталитический способ очистки газовых
выбросов от органических примесей внедрен в различных отраслях промышленности.
Однако большинству реакторов присущи недостатки: периодичность работы, низкая
производительность, отсутствие пылеочистных устройств и высокая стоимость [12].
Компактный и экономичный реактор для каталитического
дожигания отходящих газов разработан в нашем институте (рис. 10).
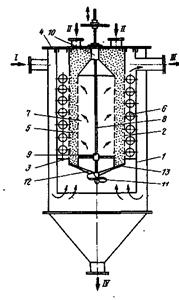
Рис. 10. Изотермический реактор:
8 — вал, 9, 10 — опоры, 11— завихритель воздуха, 12 —
опорное кольцо, 13 — направляющая опорного кольца, I—вход газов, II—загрузка
катализатора, III—выход очищенных газов, IV—выгрузка катализатора
Это аппарат циклонного типа с радиальным вводом газа,
в котором сплошная центральная труба предназначена для вывода газа, прошедшего
через слой катализатора 5 и отдавшего свое тепло, например, воде теплообменника
6. Внутри центральной трубы с образованием кольцевого зазора, ограниченного ее
стенкой, обечайкой корзины 2, кольцом 3 и крышкой 4, установлена корзина с
катализатором и примыкающий к ней трубчатый теплообменник 6; обечайки корзин 2
и 7 перфорированы. В таком реакторе одновременно протекают три процесса:
очистка газов от пыли в поле центробежных сил и на гофрах внутренней обечайки
корзины 7; каталитическое окисление органических примесей в слое катализатора
и, наконец, утилизация тепла.
Капитальные затраты на строительство подобных
реакторов, как правило, на 15—20 % меньше, степень очистки газов от пыли на
1,5—1,8 % выше. Совмещенный реактор можно разместить на площади 60—70 м2, а
промышленный реактор такой же производительности (например, 20 тыс. м3/ч)
требует не меньше 120 м2. Замену катализатора можно производить с помощью
запорного устройства без остановки реактора. На основании лабораторных
исследований подобраны дешевые катализаторы: марганцевая руда, марганцевый
агломерат и меднохромовый контакт. Реактор рекомендован для внедрения на
опытной установке шахты и на химическом заводе.
Список литературы
1. Термокаталитические реакторы для очистки газов //
Каталожный листок / Химнефтемаш. М.: ЦИНТИ, 1984.— 84 с.
2. А. с. 1060214 СССР. Реактор для проведения
каталитических процессов / А. М. Сычева, В. С. Генкин, С. И. Мельников, Н М.
Дюрик и др. // Открытия. Изобретения. 1983. № 46. С. 18, 19.
3. Беляков Б. П., Исаков И. Г., Шейко А. В.
Термические методы обезвреживания промышленных газообразных выбросов //
Промышленная и санитарная очистка газов: Обзор, информ. Сер. ХМ-14/
ХИНТИхимнефтемаш. 1983.— 21 с.
4. Ледокова Г. М., Попова Н. М., Сокольский Д. В. и
др. Термокаталитическая очистка газовых выбросов производства пластмасс //
Каталитическая очистка газов: Матер. IV Всесоюзн. конф. Ч. 2.— Алма-Ата. 1985.
С. 83—88.
5. Шафранский Е. Л., Дряхлое А. С., Калинкина Л. И. и
др. / Там же. С. 89—93.
6. А. с. 849594 СССР. Способ очистки отходящих газов /
Г. К. Боресков, Ю. Ш. Матрос, В. Г. Луговской // Открытия. Изобретения. 1982. №
14. С. 320.
7. А. с. 882056 СССР. Способ очистки отходящих газов /
Г. К- Боресков, Ю. Ш. Матрос, В. М. Пажилова и др. // Открытия. Изобретения.
1982. № 15. С. 287.
8. Катализ в промышленности / А. Слейш, У. Чоудри, Ф.
Вагнер и др.: Пер. с англ, под ред В. М. Грязнова.— М.: Мир, 1986.— 291 с.
9. Дряхлое А. С., Калинкина Л. И., Жданович Н. В. и
др. Об особенностях моделирования реактора санитарной очистки воздуха... //
Каталитическая очистка газов: Матер. III Всесоюзн. конф. Ч. I.— Новосибирск.
1981. С. 121—128.
10. МРТ 37.056.142-82. Аппараты очистки газовых
выбросов с замкнутым циклом и автономной системой управления. Унифицированные
сборочные единицы.— М.: Стандарты, 1982.— 91 с.
И. Губайдулин Р. 3., Квасов А. А., Шурин Р. М.
Современные аппараты каталитической очистки газовых выбросов // Промышленная и
санитарная очистка газов: Обзор, информ. Сер. ХМ-14. / ЦИНТИхимнефтемаш. 1985.—
29 с.
12. Торопкина Г. Н., Калинкина Л. И. Технико-экономические
показатели промышленной очистки газовых выбросов от органических веществ //
Промышленная и санитарная очистка газов: Обзор, информ. / ЦИНТИхимнефтемаш.
1983. С. 4—18.
Для подготовки данной работы были использованы
материалы с сайта http://masters.donntu.edu.ua
|